Borealis with high-barrier packaging for mechanical recycling of PP
Borealis announces the launch of a new mono-material pouch designed for recycling, with a PP content of over 95%, which will be showcased at the Plastics Recycling Show Europe (PRSE) in May. Developed in collaboration with partners along the value chain, this sustainable high-barrier packaging format offers a range of benefits for film and laminate manufacturers, as well as for brand owners and end consumers. As a mono-material PP package, it can help achieve the ambitious goals of the EU’s Packaging and Packaging Waste Regulation (PPWR) regarding recycling and waste reduction, and make meaningful use of recycling processes in line with extended producer responsibility (EPR).
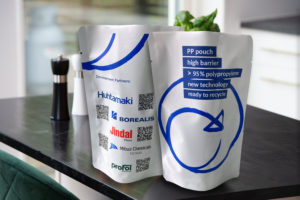
Borealis drives plastic circular economy through collaborations along the entire value chain
High-barrier packaging is designed to preserve food and protect it against moisture, oxygen, aroma loss, or light, thereby ensuring the longevity of products such as dry or powdered ingredients like coffee, milk powder, or snacks. Both producers and consumers benefit from longer shelf life and reduced food waste enabled by this high-barrier laminate pouch. Through extrusion lamination, PP cast and BOPP (biaxially oriented polypropylene) films are processed into mono-material PP laminates, which offer unique product advantages, such as high oxygen and water vapor barriers, stiffness, and excellent sealing properties.
Previously, manufacturers could produce mono-material laminates with a PP content of around 90% using adhesive lamination. The packaging solution developed through the collaboration between Borealis and its partners now allows this content to increase to over 95%. By utilizing specialized mechanical recycling streams for PP, the mono-material pouch can also supply larger amounts of high-quality recyclate suitable for the production of flexible PP packaging for non-food applications. This makes the pouch an ideal format to achieve the core goals of the PPWR: making the recycling of flexible packaging more efficient, expanding the market for recycled content, and reducing packaging waste.
*While the eco-modulated EPR fees, based on the recyclability of packaging and its recycled content, may vary across EU member states, the new mono-material pouch with over 95% PP meets the CEFLEX (Circular Economy for Flexible Packaging) definition of “compatibility with the mechanical recycling of PP.” This enables cost savings compared to traditional pouch formats made from a combination of different materials.
“In line with our mission to reinvent the fundamentals to make our lives more sustainable, our goal is also to maintain the integrity and quality of packaging materials while ensuring that the circular orientation of these purpose-driven formats continues to increase,” explains Peter Voortmans, Borealis Global Commercial Director Consumer Products. “We are very proud of this collaboration along the value chain. It provides our partners and customers with another viable and sustainable solution that helps them meet the updated requirements of the PPWR.”
The high-barrier pouch, which consists of over 95% PP, boasts excellent seal strength and hermetic closure properties thanks to the material solutions and production expertise of all partners involved in this project along the value chain. The commercially available polyolefins from the Borealis PP product portfolio for extrusion coatings and laminates ensure stable processability and excellent bond strength of the laminate. These were used together with PP-based adhesives supplied by the Mitsui Chemical Group, a leading international manufacturer of specialty chemicals, including polyolefin-based binders. As a global leader in the development and production of BOPP specialty films, Jindal Films also contributed to this innovative solution for recyclable packaging. Profol, which operates sites in Europe, America, and China and is known for its innovative cast films and lightweight PP components, provided the PP cast film for this product. The global company Huhtamaki Flexible Packaging, which offers consumer-friendly and sustainable packaging solutions, contributed the innovative composite film through extrusion lamination for the new mono-material PP pouch.